OUR QUALITY MANAGEMENT SYSTEM
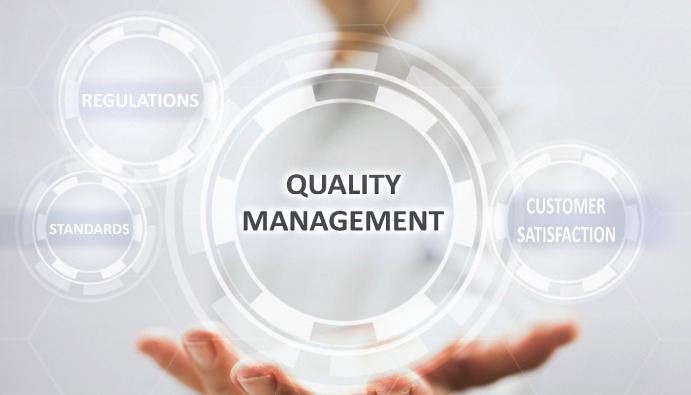
Our Quality Management SYSTEM
Through our quality management process our equipment is scrupulously evaluated by our highly qualified technical team to meet manufacturer’s specifications and global standards, so you can efficiently and safely meet the needs of your patients.
OUR QUALITY MANAGEMENT PROCESS
- Remove all cover panels
- Remove all boards and inspect for damages and wear including burned or brown spots
- All boards are replaced as necessary
- Inspect high voltage cables for cuts, arching, and bad connections and replaced if necessary
- All casters & locks inspected and repaired/ replaced as needed
- Inspect X-Ray tube, recalibrate or replace if necessary
- Inspect Image Intensifier in all tri modes
- Image Intensifier recalibrated & replaced if needed
- Electrical motors inspected, calibrated & lubricated where needed
- CCD camera is inspected, calibrated, and replaced if needed
- Lubricate all bearings
- All areas needing lubrication are re-lubricated.
- Inspect CRT’s/ Monitors for burn-in or poor resolution, to include the power supplies if and as needed
- Inspect all knobs and buttons – set to be functioning according to manufacturer specifications
- Inspect all motor drives, i.e. – tilt, up/down, in/out, etc.
- Complete electrical safety check
- Inspect umbilical cable from monitor cart to C-arm for broken wires and missing pins, replace if necessary
- Prime, sand and re-paint complete system
- Equipment is brought to manufacturer specifications
Talk to us
Have any questions? We are always open to talk about your business, new projects, creative opportunities and how we can help you.